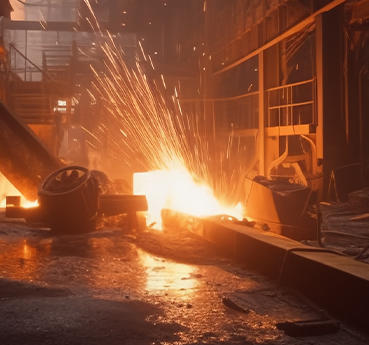
La forja es un método de procesamiento que utiliza maquinaria de forja para aplicar presión a las palanquillas de metal, provocando que sufran deformación plástica para obtener piezas forjadas con ciertas propiedades mecánicas, formas y tamaños. Es uno de los dos componentes principales de la forja (forja y estampado). La forja puede eliminar defectos como la porosidad de la fundición en el proceso de fundición de metales, optimizar la microestructura y, debido a la preservación de líneas de flujo de metal completas, las propiedades mecánicas de las piezas forjadas son generalmente mejores que las de las piezas fundidas del mismo material. Las piezas importantes de maquinaria relacionada con cargas elevadas y condiciones de trabajo severas, excepto las formas simples que se pueden laminar en placas, perfiles o piezas soldadas, están hechas en su mayoría de piezas forjadas.
La temperatura de deformación de los materiales de forja.
La temperatura inicial de recristalización del acero se divide por 800 ℃, y el forjado en caliente se produce por encima de 800 ℃; La forja entre 300 y 800 ℃ se llama forja en caliente o forja semicaliente, y la forja a temperatura ambiente se llama forja en frío. Las piezas forjadas utilizadas en la mayoría de las industrias son la forja en caliente, mientras que la forja en caliente y en frío se utiliza principalmente para forjar piezas como automóviles y maquinaria en general. La forja en frío y en caliente puede ahorrar materiales de forma eficaz.
La categoría de forja.
Según la temperatura de forjado, se puede dividir en forjado en caliente, forjado en caliente y forjado en frío.
Según el mecanismo de formación, la forja se puede dividir en forja libre, forja con matriz, laminación de anillos y forja especial.
1. Forja libre. El método de procesamiento de forja se refiere al uso de herramientas universales simples o la aplicación directa de fuerzas externas entre los yunques superior e inferior del equipo de forja para deformar el tocho y obtener la forma geométrica y la calidad interna requeridas. Las piezas forjadas producidas mediante el método de forja libre se denominan forjas libres. La forja libre produce principalmente pequeños lotes de piezas forjadas, utilizando equipos de forja como martillos y prensas hidráulicas para dar forma y procesar las piezas en bruto y obtener piezas forjadas calificadas. Los procesos básicos de forjado libre incluyen recalcado, alargamiento, punzonado, corte, doblado, torsión, desplazamiento y forjado. La forja libre adopta el método de forja en caliente.
2. Forja por troquel. La forja con matriz se puede dividir en forja con matriz abierta y forja con matriz cerrada. Los tochos de metal se forman mediante deformación por compresión en la cámara de la matriz de forjado con una determinada forma para obtener piezas forjadas. La forja con matriz se utiliza generalmente para producir piezas con pesos pequeños y lotes de gran tamaño.
La forja con matriz se puede dividir en forja con matriz en caliente, forja en caliente y forja en frío. La forja en caliente y la forja en frío son las direcciones de desarrollo futuro de la forja con matrices y también representan el nivel de tecnología de forja. Según la clasificación del material, la forja con matrices también se puede dividir en forja con matrices de metal negro, forja con matrices de metales no ferrosos y conformación de productos en polvo. Como sugiere el nombre, los materiales son metales negros como el acero al carbono, metales no ferrosos como el cobre y el aluminio y materiales pulvimetalúrgicos. La extrusión debe pertenecer a la forja con matriz y se puede dividir en extrusión de metales pesados y extrusión de metales ligeros. Cabe señalar que el tocho no se puede restringir por completo. Por lo tanto, es necesario controlar estrictamente el volumen de la palanquilla, controlar la posición relativa de la matriz de forja y medir las piezas forjadas, esforzándose por reducir el desgaste de la matriz de forja.
3. Anillo de molienda. El laminado de anillos se refiere a la producción de piezas circulares con diferentes diámetros utilizando equipos especializados, como máquinas laminadoras de anillos, y también se utiliza para producir piezas con forma de rueda, como ruedas de automóviles y ruedas de tren.
4. Forja especial. La forja especial incluye métodos de forja como forja por rodillo, laminado en cuña cruzada, forja radial y forja con matriz líquida, todos los cuales son más adecuados para producir ciertas piezas con formas especiales.
Por ejemplo, el forjado con rodillos puede servir como un proceso de preformado eficaz, reduciendo significativamente la presión de formado posterior; El laminado en cuña cruzada puede producir piezas como bolas de acero y ejes de transmisión; La forja radial puede producir piezas forjadas grandes, como cañones de armas y ejes escalonados.
morir forja
Según el modo de movimiento de la matriz de forja, la forja se puede dividir en forja oscilante, forja rotativa oscilante, forja por rodillo, laminado en cuña transversal, laminado en anillo y laminado oblicuo. La forja rotativa, la forja rotativa y la forja de precisión también se pueden utilizar para el anillo de prensa hidráulica de forja de aviación de servicio pesado de 400 MN (40000 toneladas) en China. Para mejorar la tasa de utilización de materiales, se pueden utilizar el forjado por rodillos y el laminado transversal como procesos anteriores para procesar materiales delgados. La forja rotativa, al igual que la forja libre, también se forma localmente y su ventaja es que puede formarse incluso bajo fuerzas de forja más pequeñas en comparación con el tamaño de la forja. Este método de forja, incluida la forja libre, implica la expansión de materiales desde las proximidades de la superficie del molde hasta la superficie libre durante el procesamiento, lo que dificulta garantizar la precisión. Por lo tanto, al controlar la dirección del movimiento de la matriz de forjado y el proceso de forjado giratorio con una computadora, se pueden obtener productos de alta precisión y formas complejas con menor fuerza de forjado, como la producción de piezas forjadas con múltiples variedades y grandes tamaños de álabes de turbinas de vapor. .
El movimiento del molde y los grados de libertad del equipo de forja son inconsistentes. Según las características de las limitaciones de deformación en el punto muerto inferior, el equipo de forja se puede dividir en las siguientes cuatro formas:
1. Forma de fuerza de forjado limitada: una prensa hidráulica que impulsa directamente el control deslizante con presión de aceite.
2. Método de límite de cuasi carrera: una prensa hidráulica que acciona el mecanismo de biela del cigüeñal mediante presión hidráulica.
3. Método de limitación de carrera: una prensa mecánica con manivela, biela y mecanismo de cuña que acciona el control deslizante.
4. Método de limitación de energía: utilice el mecanismo en espiral del tornillo y la prensa de fricción. Para lograr una alta precisión durante las pruebas en caliente de prensas hidráulicas de forja de aviación de servicio pesado, se debe prestar atención a evitar la sobrecarga en el punto muerto inferior, controlando la velocidad y la posición del molde. Porque estos tendrán un impacto en la tolerancia, la precisión de la forma y la vida útil de las piezas forjadas. Además, para mantener la precisión, también se debe prestar atención al ajuste del espacio libre entre los rieles guía deslizantes, asegurando la rigidez, ajustando el punto muerto inferior y utilizando dispositivos de transmisión auxiliares.
Control deslizante forjado
Los controles deslizantes de forja se pueden dividir en movimientos verticales y horizontales (utilizados para forjar piezas delgadas, lubricación, enfriamiento y forja de piezas de producción de alta velocidad), y se pueden usar dispositivos de compensación para aumentar el movimiento en otras direcciones. Los métodos anteriores son diferentes, y la fuerza de forjado, el proceso, la tasa de utilización del material, la producción, la tolerancia dimensional y el método de lubricación y enfriamiento necesarios para forjar con éxito el producto tipo disco grande son todos diferentes. Estos factores también son factores que afectan el nivel de automatización.Materiales utilizados para la forja.
Los principales materiales utilizados para la forja son el acero al carbono y los aceros aleados con diversas composiciones, seguidos del aluminio, magnesio, cobre, titanio y sus aleaciones. El estado original de los materiales incluye barras, lingotes, polvos metálicos y metales líquidos. La relación entre el área de la sección transversal de un metal antes de la deformación y el área de la sección transversal después de la deformación se denomina relación de forja. La selección correcta de la relación de forjado, la temperatura de calentamiento y el tiempo de aislamiento razonables, las temperaturas de forjado inicial y final razonables, la cantidad de deformación razonable y la velocidad de deformación están estrechamente relacionadas con la mejora de la calidad del producto y la reducción de costos. Generalmente, las piezas forjadas pequeñas y medianas utilizan barras redondas o cuadradas como palanquillas. La estructura del grano y las propiedades mecánicas del material de la barra son uniformes y buenas, con forma y tamaño precisos, buena calidad de la superficie y producción en masa fácil de organizar. Siempre que la temperatura de calentamiento y las condiciones de deformación estén razonablemente controladas, se pueden forjar piezas forjadas de alto rendimiento sin una deformación significativa de la forja. Los lingotes sólo se utilizan para piezas forjadas grandes. El lingote es una estructura fundida con grandes cristales columnares y un centro suelto. Por lo tanto, es necesario romper los cristales columnares en granos finos mediante una gran deformación plástica y compactarlos sin apretar para obtener estructura metálica y propiedades mecánicas. Las preformas de pulvimetalurgia fabricadas mediante prensado y cocción se pueden forjar en piezas forjadas en polvo sin rebabas en estado caliente. La densidad del polvo de forja es cercana a la de las piezas forjadas con matrices generales, con buenas propiedades mecánicas y alta precisión, lo que puede reducir el procesamiento de corte posterior. La estructura interna de las piezas forjadas en polvo es uniforme sin segregación y puede usarse para fabricar engranajes pequeños y otras piezas de trabajo. Sin embargo, el precio del polvo es mucho más alto que el de las barras normales y su aplicación en la producción está sujeta a ciertas limitaciones. Al aplicar presión estática al metal líquido vertido en la cavidad del molde, que se solidifica, cristaliza, fluye, sufre deformación plástica y se forma bajo presión, se puede obtener la forma y el rendimiento requeridos de la forja. La forja de metal líquido es un método de formación que se encuentra entre la fundición a presión y la forja, especialmente adecuado para piezas complejas de paredes delgadas que son difíciles de formar en la forja general. Además de los materiales comunes como el acero al carbono y el acero aleado con diversas composiciones, seguidos del aluminio, magnesio, cobre, titanio y sus aleaciones, las aleaciones de deformación de aleaciones de alta temperatura a base de hierro, aleaciones de alta temperatura a base de níquel, y las aleaciones de alta temperatura a base de cobalto también se completan mediante forja o laminación. Sin embargo, estas aleaciones tienen zonas plásticas relativamente estrechas, por lo que la dificultad de forja es relativamente alta. Los diferentes materiales tienen requisitos estrictos en cuanto a temperatura de calentamiento, temperatura de forjado de apertura y temperatura de forjado final.
Flujo del proceso de forja
Los diferentes métodos de forja tienen diferentes procesos, entre los cuales el proceso de forja en caliente es el más largo y el orden general es: corte de forja en blanco; Calentamiento de palanquillas de forja; Preparación en blanco para forja en rollo; Conformación por forja; Los bordes de corte; Puñetazos; Corrección; Inspección intermedia, comprobando las dimensiones y defectos superficiales de las piezas forjadas; Tratamiento térmico de piezas forjadas para eliminar la tensión de forja y mejorar el rendimiento del corte de metales; Limpieza, principalmente para eliminar incrustaciones de óxido superficial; Corrección; Inspección: Generalmente, las piezas forjadas deben someterse a una inspección de apariencia y dureza, mientras que las piezas forjadas importantes también deben someterse a análisis de composición química, propiedades mecánicas, pruebas de tensión residual y pruebas no destructivas.
Características de las forjas
En comparación con las piezas fundidas, el metal puede mejorar su microestructura y propiedades mecánicas después del procesamiento de forjado. Después del trabajo en caliente y la deformación mediante el método de forjado, la estructura de fundición se transforma de dendritas gruesas y granos columnares a estructuras recristalizadas equiaxiales con tamaños más finos y uniformes debido a la deformación y recristalización del metal. Esto provoca la segregación original, porosidad, inclusión de escoria y otras compactaciones y soldaduras en el lingote de acero, haciendo la estructura más compacta y mejorando la plasticidad y propiedades mecánicas del metal. Las propiedades mecánicas de las piezas fundidas son inferiores a las de las piezas forjadas del mismo material. Además, el procesamiento de forjado puede garantizar la continuidad de la estructura de fibra metálica, manteniendo la estructura de fibra de la forja consistente con la forma de la forja. La línea de flujo de metal está completa, lo que puede garantizar que las piezas tengan buenas propiedades mecánicas y una larga vida útil. Las piezas forjadas producidas mediante forjado de precisión, extrusión en frío, extrusión en caliente y otros procesos son incomparables con las piezas fundidas. Las piezas forjadas son objetos a los que se les da forma mediante deformación plástica para alcanzar la forma requerida o la fuerza de compresión adecuada cuando el metal se somete a presión. Este poder generalmente se logra mediante el uso de un martillo o presión. El proceso de forjado crea estructuras de partículas exquisitas y mejora las propiedades físicas del metal. En el uso práctico de componentes, un diseño correcto puede garantizar que el flujo de partículas esté en la dirección de la presión principal. Las piezas fundidas son objetos formados por metal que se obtienen mediante diversos métodos de fundición, es decir, el metal líquido fundido se inyecta en moldes preparados previamente mediante vertido, inyección, succión u otros métodos de fundición, se enfría y luego se somete a remoción de arena, limpieza y posproducción. -tratamiento para obtener objetos con una determinada forma, tamaño y prestaciones.
Análisis de nivel de forja.
La industria china de la forja se ha desarrollado sobre la base de la introducción, asimilación y absorción de tecnología extranjera. Después de años de desarrollo y transformación tecnológicos, el nivel técnico de las empresas de la industria ha mejorado enormemente, incluido el diseño de procesos, la tecnología de forjado, la tecnología de tratamiento térmico, la tecnología de mecanizado, las pruebas de productos y otros aspectos.
(1) Los fabricantes avanzados en el diseño de procesos generalmente adoptan tecnología de simulación por computadora de procesamiento en caliente, diseño de procesos asistido por computadora y tecnología virtual, mejorando el nivel de diseño de procesos y las capacidades de fabricación de productos. Introducir y aplicar programas de simulación como DATAFOR, GEMARC/AUTOFORGE, DEFORM, LARSTRAN/SHAPE y THERMOCAL para lograr el control de procesos de diseño por computadora y procesamiento térmico.
(2) La mayoría de las prensas hidráulicas con tecnología de forjado de 40 MN y más están equipadas con 100-400 t. m operadores principales de forja y 20-40t. m operadores auxiliares. Un número considerable de operadores utiliza el control por computadora para lograr un control integral del proceso de forjado, lo que permite controlar la precisión del forjado dentro de ± 3 mm. La medición en línea de piezas forjadas utiliza dispositivos de medición de tamaño por láser.
(3) El objetivo de la tecnología de tratamiento térmico es mejorar la calidad del producto, mejorar la eficiencia del tratamiento térmico, ahorrar energía y proteger el medio ambiente. Si el proceso de calentamiento del horno de calentamiento y del horno de tratamiento térmico se controla mediante una computadora, el quemador se puede controlar para lograr el ajuste automático de la combustión, la temperatura del horno, el encendido automático y la gestión de los parámetros de calentamiento; Aprovechamiento del calor residual, hornos de tratamiento térmico equipados con cámaras de combustión regenerativas, etc.; Mediante el uso de tanques de aceite de enfriamiento de polímeros con baja capacidad de contaminación y control de enfriamiento efectivo, varios medios de enfriamiento a base de agua están reemplazando gradualmente al aceite de enfriamiento tradicional.
(4) La proporción de máquinas herramienta CNC en la industria de la tecnología de mecanizado está aumentando gradualmente. Algunas empresas del sector cuentan con centros de mecanizado y están equipadas con maquinaria de mecanizado propia según diferentes tipos de productos, como centros de mecanizado de cinco coordenadas, máquinas de mecanizado de cuchillas, molinos de rodillos, tornos de rodillos, etc.
(5) Medidas de garantía de calidad: algunas empresas nacionales se han equipado con los últimos instrumentos de detección y tecnologías de prueba, modernos sistemas de prueba ultrasónicos automatizados con procesamiento de datos controlado por computadora y varios sistemas de prueba ultrasónicos automáticos especializados para completar la certificación de varios sistemas de calidad. La tecnología de producción clave de piezas forjadas de engranajes pesados de alta velocidad se ha ido superando continuamente y, sobre esta base, se ha logrado la producción industrial. Gracias a la introducción de tecnología de producción avanzada y equipos clave del extranjero, China ha podido diseñar y fabricar por su cuenta equipos de producción para piezas forjadas de engranajes de alta velocidad y servicio pesado. Estos equipos se han acercado al nivel avanzado internacional y la mejora del nivel de tecnología y equipos ha promovido efectivamente el desarrollo de la industria de forja nacional.
La importancia de la forja
La producción de forja es uno de los principales métodos de procesamiento para proporcionar piezas en bruto de piezas mecánicas en la industria de fabricación mecánica. Mediante la forja, no sólo se puede obtener la forma de las piezas mecánicas, sino que también se puede mejorar la estructura interna del metal y se pueden mejorar las propiedades mecánicas y físicas del metal. Generalmente, las piezas mecánicas importantes con altos requisitos y tensiones se fabrican utilizando métodos de producción de forja. Componentes importantes como ejes de generadores de turbinas, rotores, impulsores, palas, anillos de retención, grandes columnas de prensas hidráulicas, cilindros de alta presión, rodillos de laminación de acero, cigüeñales de motores de combustión interna, bielas, engranajes, cojinetes y artillería en la defensa nacional. La industria se produce todos a través de la forja. [7] Por lo tanto, la producción de forja se utiliza ampliamente en industrias como la metalurgia, la minería, los automóviles, los tractores, la maquinaria de cosecha, el petróleo, la industria química, la aviación, la aeroespacial, las armas, etc. Incluso en la vida diaria, la producción de forja también juega un papel importante. . En cierto sentido, la producción anual de piezas forjadas, la proporción de piezas forjadas en la producción total de piezas forjadas, así como el tamaño y la propiedad del equipo de forja, reflejan hasta cierto punto el nivel industrial de un país.